coal фрезерование classifier adjustment
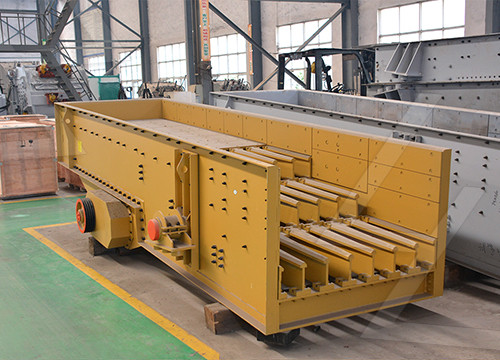
(PDF) INVESTIGATION ON CLASSIFICATION
2020年7月14日 To attain maximum combustion efficiency in boilers, a minimal amount of coarse particle distribution at the burner should be achieved. Therefore, classification of coal dust is crucial in...
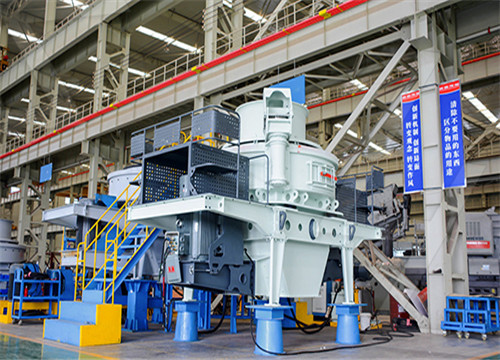
INVESTIGATION ON CLASSIFICATION EFFICIENCY FOR COAL
Coal classification is an essential factor to improve the overall efficiency of the thermal power plant and reduce the concentration of the pollutant emissions from boilers such as
进一步探索Classification of coal fired power plants 9 Download Table Electrical Area Classification in Coal-Fired Power Plants 根据热度为您推荐•反馈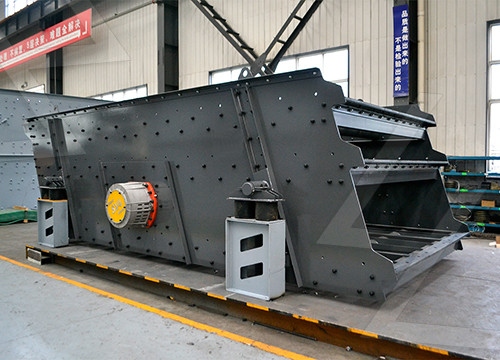
Numerical and experimental analysis of pulverized coal
2014年10月1日The assumption of a decreasing regrind outlet of coal flow rate by plate adjustment in the classifier for D-21 appears to be sufficient to increase total coal flow
作者: Selçuk Ataş, Uğur Tekir, Mehmed Akif Paksoy, Ahmet Çelik, Metin Çam, Tahsin Sevgel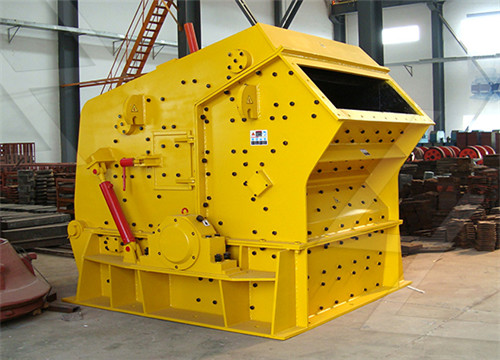
13045 Coal Distributor Paper:Layout 1 Babcock Power
This stone presents a newly-developed technology for correcting coal flow in individual coal pipes from a pulverizer classifier without changing PA flow distribution balance.
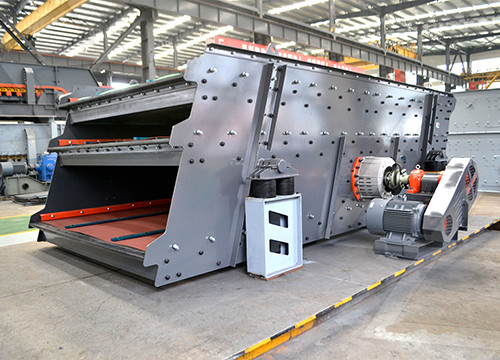
Industrial Coal Pulverizer Model Simulation and
2018年1月1日This stone describes the first principle based energy and mass balance mathematical models of 1) Static-classifier, and 2) Dynamic-classifier types of
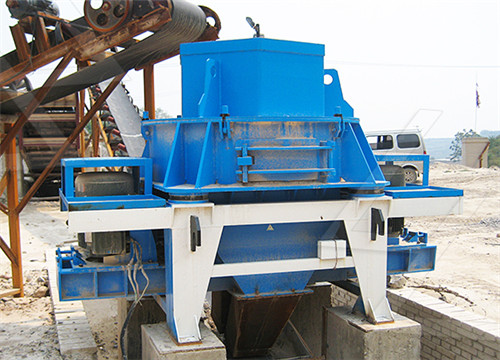
Dynamic classifiers improve pulverizer performance and
2007年7月15日By adding a dynamic classifier to the pulverizers, you can better control coal particle sizing and fineness—and increase pulverizer capacity to boot. NewsTechnology for the Global Energy Industry
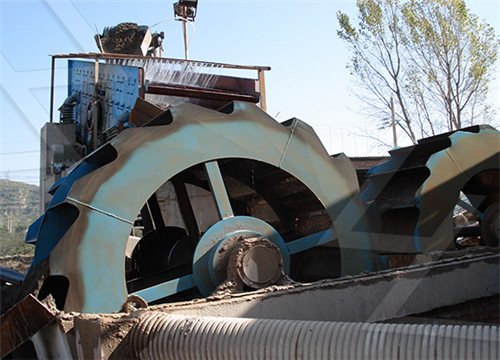
The Performance of a Static Coal Classifier and Its
2012年10月19日Experiments were conducted at air flow rates of 1.41-1.71kg/s and air fuel ratios of 4.8-10 with classifier vane angle adjustment (30°- 60°) and inlet swirl umbers

CFD based investigations into optimization of coal
2009年9月1日In this investigation, numerical simulations of a typical pf coal based pulveriser have been carried out for different classifier vane settings to evaluate uniform
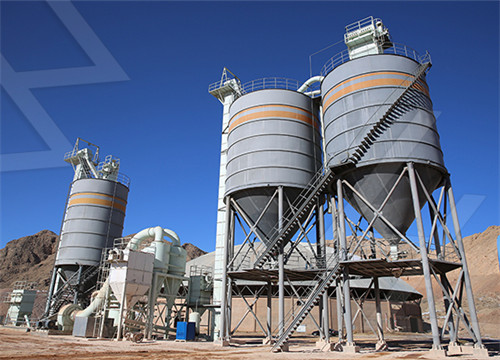
CPRI Online Coal Flow Balancing and Fineness
ABSTRACT: The stone describes the beneficial application of online coal flow measurement and control and online coal fineness measurement for optimization of the combustion
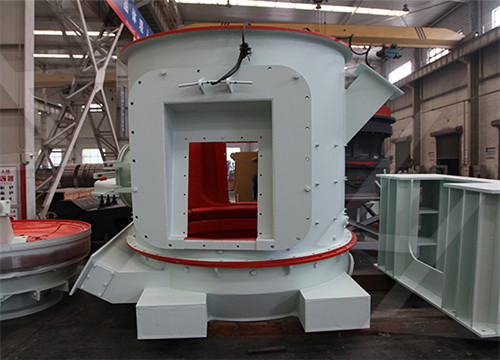
(PDF) INVESTIGATION ON CLASSIFICATION
2020年7月14日 To attain maximum combustion efficiency in boilers, a minimal amount of coarse particle distribution at the burner should be achieved. Therefore, classification of coal dust is crucial in...
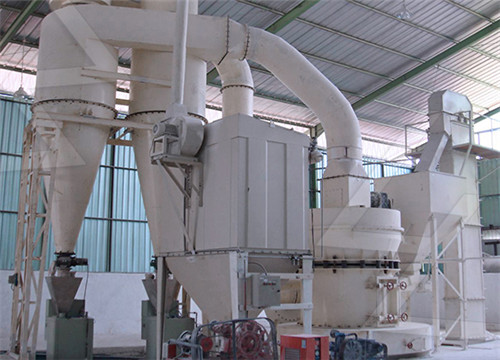
Coal and gas outbursts prediction based on
2021年7月13日Due to the severity and great harm of coal and gas outbursts accidents, outbursts prediction becomes very necessary; the stone presents a hybrid prediction model of feature extraction and
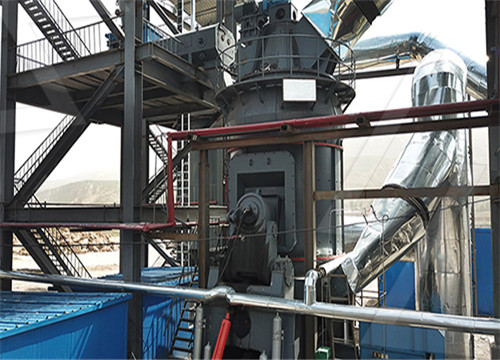
INVESTIGATION ON CLASSIFICATION EFFICIENCY FOR COAL
the spiral guide vanes on the coal classification efficiency [5, 6]. It is worth to mention that the optimum quality of classification for coals such as lignite is achieved when 70% of coal particles exiting the classifier is smaller than 75 μm [7, 8] . Other than that, the optimum quality of classification is achieved only when 80% of the
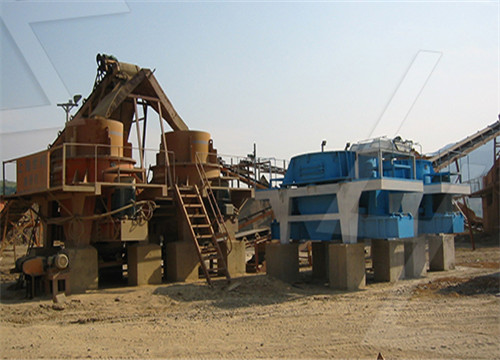
Industrial Coal Pulverizer Model Simulation and Parametric
2018年1月1日This stone describes the first principle based energy and mass balance mathematical models of 1) Static-classifier, and 2) Dynamic-classifier types of industrial coal-pulverizers.
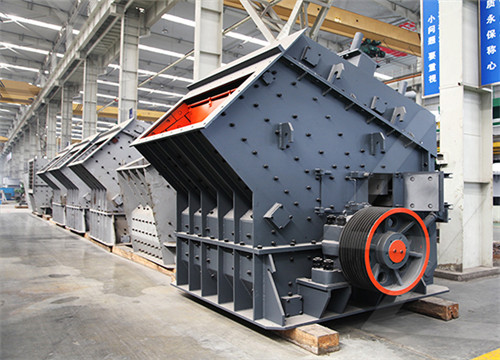
CFD based investigations into optimization of coal
2009年9月1日Experimental data can be observed that feeding Berau coal having the characteristics of Sub-bituminous coal with total moisture of 21.42% Wt and HGI 50, by setting MAFR is (1,8:1), and classifier
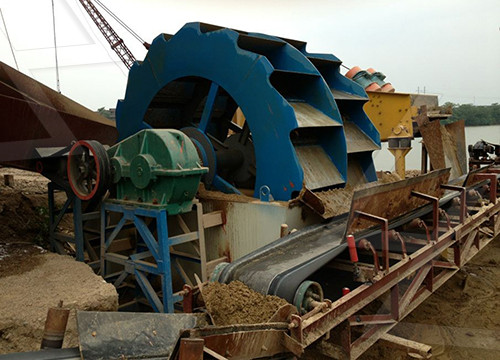
The Performance of a Static Coal Classifier and Its
2012年10月19日Experiments were conducted at air flow rates of 1.41-1.71kg/s and air fuel ratios of 4.8-10 with classifier vane angle adjustment (30°- 60°) and inlet swirl umbers (S) of 0.49 1.
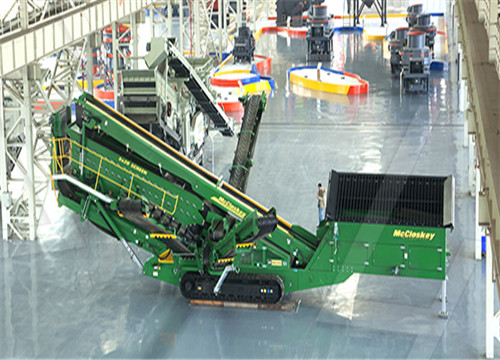
Improved Coal Fineness Improves Performance, Reduces Emissions
2011年10月1日The classifier inlet conditions were based upon actual coal fineness test results from a pulverizer with a plugged classifier reject section. Figures 5-9, provide a brief comparison of the
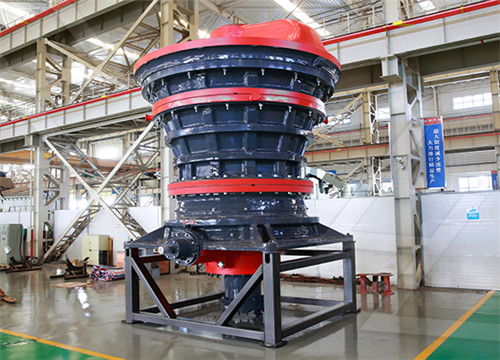
Dynamic classifiers improve pulverizer performance
2007年7月15日Dynamic classifiers can increase both fineness and capacity, but to a lesser extent than a system optimized to increase one or the other. Again, experience with vertical-shaft pulverizers at coal
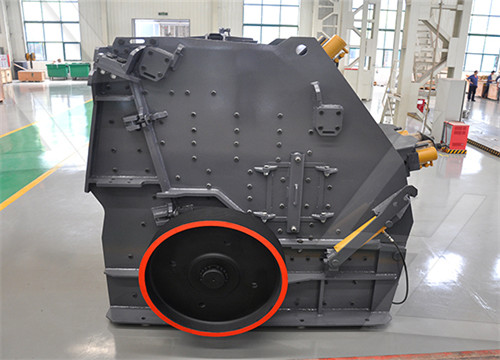
Comparison of Three Types of Coal Pulverizers Babcock Power
Properly sized pulverized coal exits the classifier into coal piping for transport to the furnace. Oversized pro- duct is, however, separated and returned to the mill for further grinding. There is minimal metal-to-metal contact of the grinding elements in the BTM resulting in very little wear and low maintenance. The mill heads are cast integral with
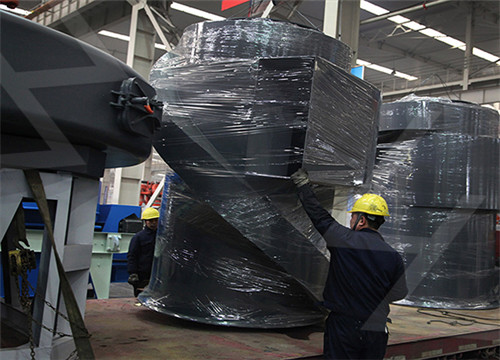
CPRI Online Coal Flow Balancing and Fineness Adjustment
Additionally, the mill and the classifier are adjusted according to the readings of the coal flow and the size spectrum. 1.0 INTRODUCTION The pulverized-fuel balance, air fuel ratio and particle size spectrum are key parameters for the optimization of the combustion process for many large scale fossil and biomass fired boilers.

(PDF) INVESTIGATION ON CLASSIFICATION
2020年7月14日 To attain maximum combustion efficiency in boilers, a minimal amount of coarse particle distribution at the burner should be achieved. Therefore, classification of coal dust is crucial in...
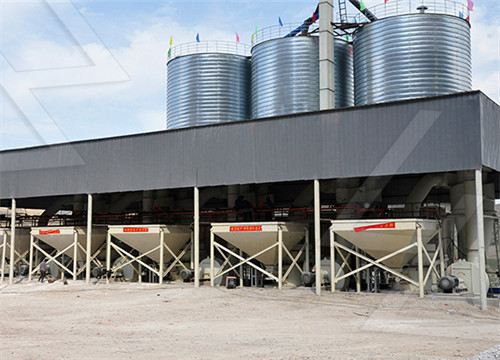
Coal and gas outbursts prediction based on
2021年7月13日Due to the severity and great harm of coal and gas outbursts accidents, outbursts prediction becomes very necessary; the stone presents a hybrid prediction model of feature extraction and
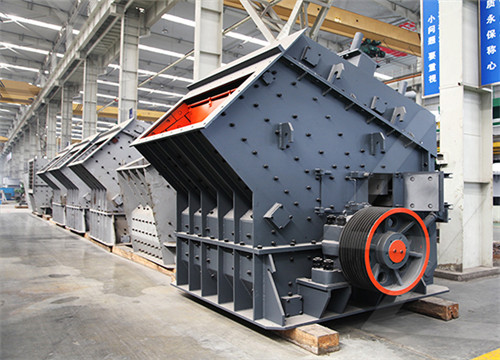
INVESTIGATION ON CLASSIFICATION EFFICIENCY FOR COAL
Coal classification is an essential factor to improve the overall efficiency of the thermal power plant and reduce the concentration of the pollutant emissions from boilers such as the unburned ash, NOx, SOx and CO [3, 4].
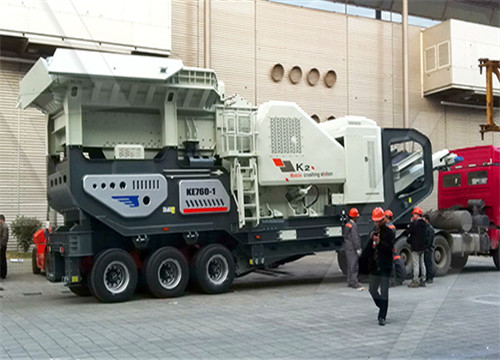
Experimental study effect of classifier pulverizer opening
2019年12月10日In this experimental, the effects of opening classifier vane settings and primary airflow to coal fineness particle size and coal flow in coal pipe distribution were measured by using dirty pitot air test dan isokinetic coal sampling. Five different position opening of classifier vane settings and three variations different of primary air-fuel ratio
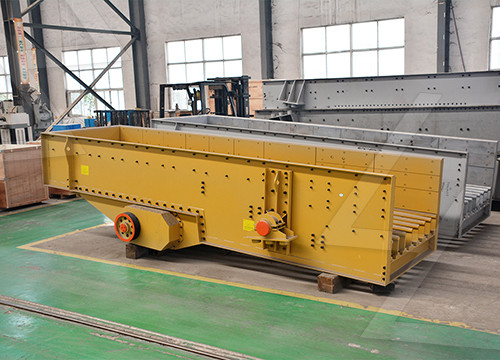
CFD based investigations into optimization of coal
2009年9月1日Experimental data can be observed that feeding Berau coal having the characteristics of Sub-bituminous coal with total moisture of 21.42% Wt and HGI 50, by setting MAFR is (1,8:1), and classifier
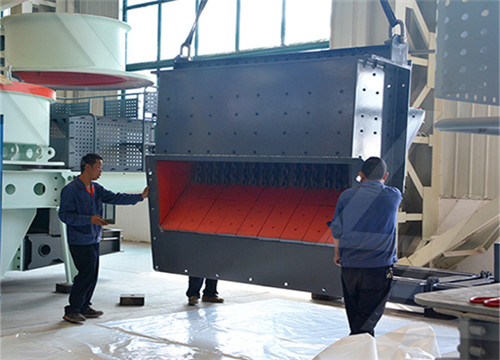
Improved Coal Fineness Improves Performance, Reduces Emissions
2011年10月1日The classifier inlet conditions were based upon actual coal fineness test results from a pulverizer with a plugged classifier reject section. Figures 5-9, provide a brief comparison of the
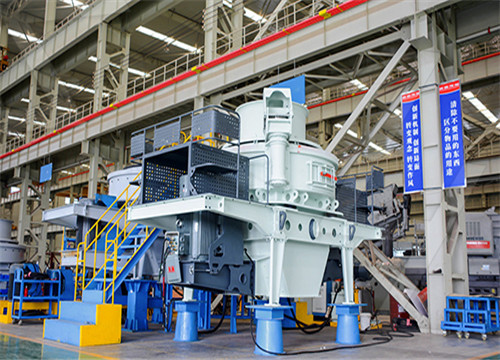
Dynamic classifiers improve pulverizer performance
2007年7月15日Dynamic classifiers can increase both fineness and capacity, but to a lesser extent than a system optimized to increase one or the other. Again, experience with vertical-shaft pulverizers at coal
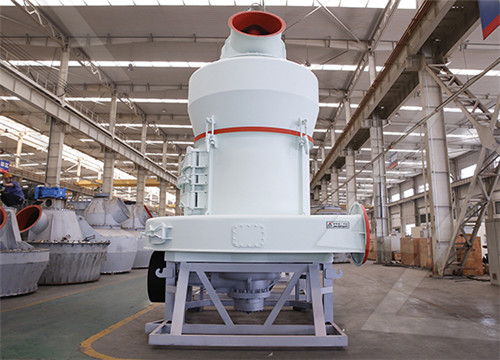
Segregation of coal particles in air classifier: Effect of
2018年5月29日The assumption of a decreasing regrind outlet of coal flow rate by plate adjustment in the classifier for D-21 appears to be sufficient to increase total coal flow rate to the burners. In the
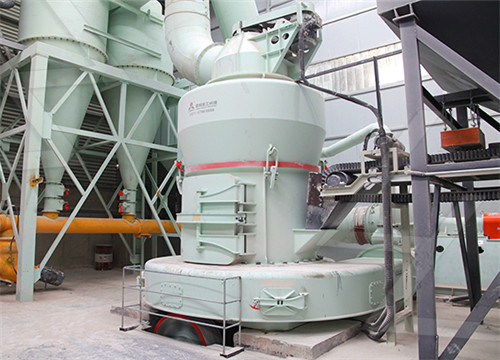
Comparison of Three Types of Coal Pulverizers Babcock Power
Properly sized pulverized coal exits the classifier into coal piping for transport to the furnace. Oversized pro- duct is, however, separated and returned to the mill for further grinding. There is minimal metal-to-metal contact of the grinding elements in the BTM resulting in very little wear and low maintenance. The mill heads are cast integral with
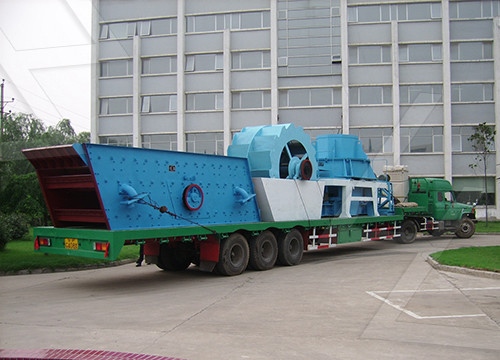
CPRI Online Coal Flow Balancing and Fineness Adjustment
Additionally, the mill and the classifier are adjusted according to the readings of the coal flow and the size spectrum. 1.0 INTRODUCTION The pulverized-fuel balance, air fuel ratio and particle size spectrum are key parameters for the optimization of the combustion process for many large scale fossil and biomass fired boilers.
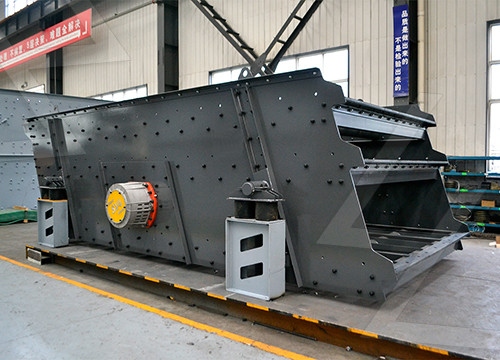
Numerical and experimental analysis of pulverized coal
2014年10月1日The assumption of a decreasing regrind outlet of coal flow rate by plate adjustment in the classifier for D-21 appears to be sufficient to increase total coal flow
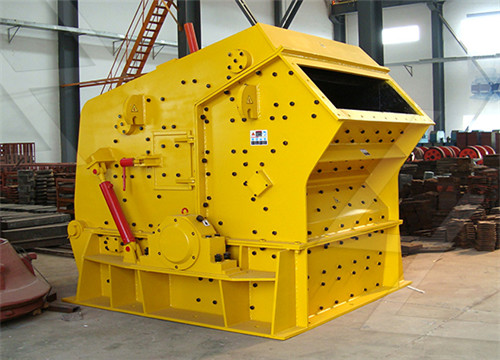
13045 Coal Distributor Paper:Layout 1 Babcock Power
This stone presents a newly-developed technology for correcting coal flow in individual coal pipes from a pulverizer classifier without changing PA flow distribution balance.
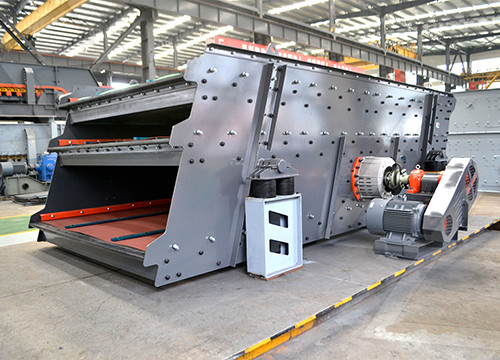
Industrial Coal Pulverizer Model Simulation and
2018年1月1日This stone describes the first principle based energy and mass balance mathematical models of 1) Static-classifier, and 2) Dynamic-classifier types of
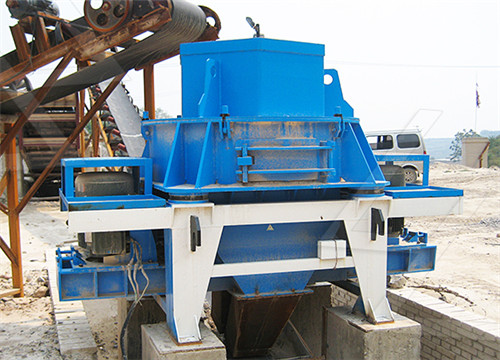
Dynamic classifiers improve pulverizer performance and
2007年7月15日By adding a dynamic classifier to the pulverizers, you can better control coal particle sizing and fineness—and increase pulverizer capacity to boot. NewsTechnology for the Global Energy Industry
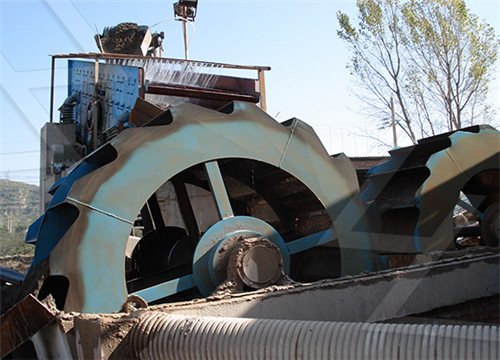
The Performance of a Static Coal Classifier and Its
2012年10月19日Experiments were conducted at air flow rates of 1.41-1.71kg/s and air fuel ratios of 4.8-10 with classifier vane angle adjustment (30°- 60°) and inlet swirl umbers

CFD based investigations into optimization of coal
2009年9月1日In this investigation, numerical simulations of a typical pf coal based pulveriser have been carried out for different classifier vane settings to evaluate uniform
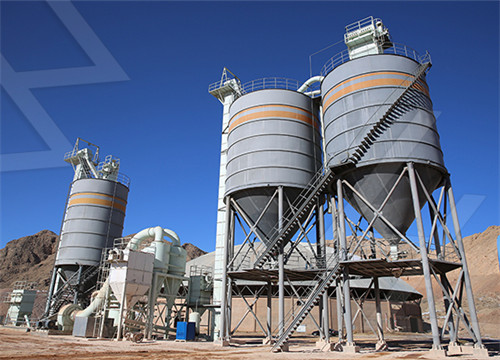
CPRI Online Coal Flow Balancing and Fineness
ABSTRACT: The stone describes the beneficial application of online coal flow measurement and control and online coal fineness measurement for optimization of the combustion
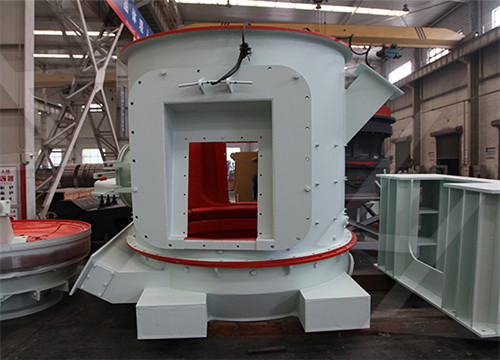
(PDF) INVESTIGATION ON CLASSIFICATION
2020年7月14日 To attain maximum combustion efficiency in boilers, a minimal amount of coarse particle distribution at the burner should be achieved. Therefore, classification of coal dust is crucial in...
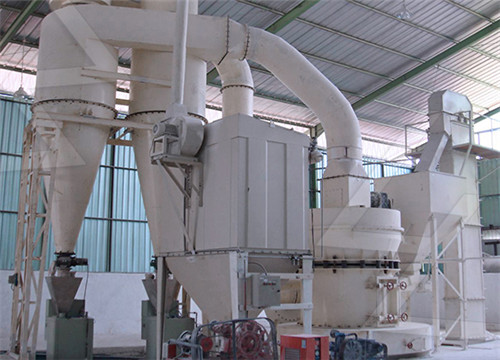
Coal and gas outbursts prediction based on
2021年7月13日Due to the severity and great harm of coal and gas outbursts accidents, outbursts prediction becomes very necessary; the stone presents a hybrid prediction model of feature extraction and
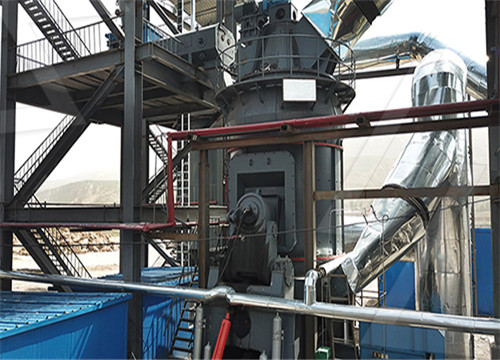
INVESTIGATION ON CLASSIFICATION EFFICIENCY FOR COAL
the spiral guide vanes on the coal classification efficiency [5, 6]. It is worth to mention that the optimum quality of classification for coals such as lignite is achieved when 70% of coal particles exiting the classifier is smaller than 75 μm [7, 8] . Other than that, the optimum quality of classification is achieved only when 80% of the
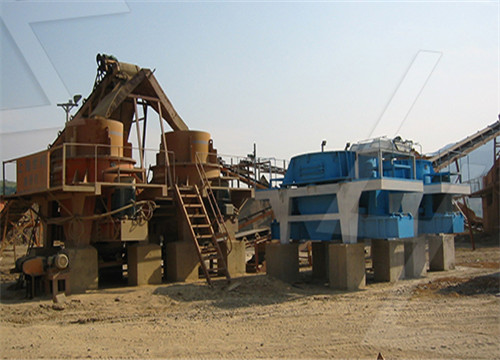
Industrial Coal Pulverizer Model Simulation and Parametric
2018年1月1日This stone describes the first principle based energy and mass balance mathematical models of 1) Static-classifier, and 2) Dynamic-classifier types of industrial coal-pulverizers.
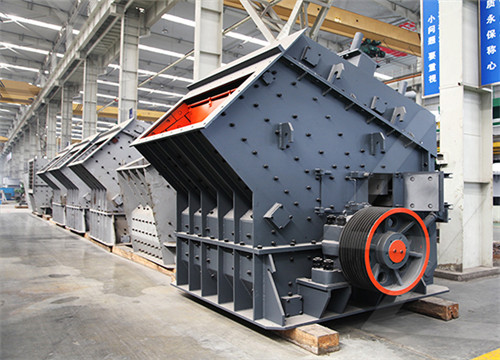
CFD based investigations into optimization of coal
2009年9月1日Experimental data can be observed that feeding Berau coal having the characteristics of Sub-bituminous coal with total moisture of 21.42% Wt and HGI 50, by setting MAFR is (1,8:1), and classifier
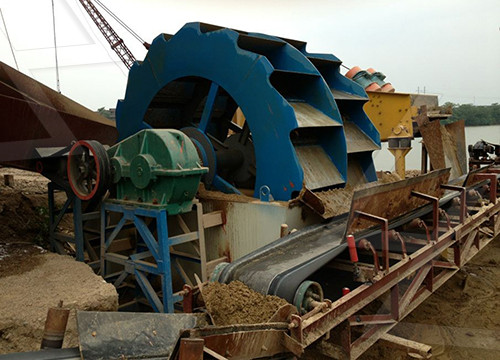
The Performance of a Static Coal Classifier and Its
2012年10月19日Experiments were conducted at air flow rates of 1.41-1.71kg/s and air fuel ratios of 4.8-10 with classifier vane angle adjustment (30°- 60°) and inlet swirl umbers (S) of 0.49 1.
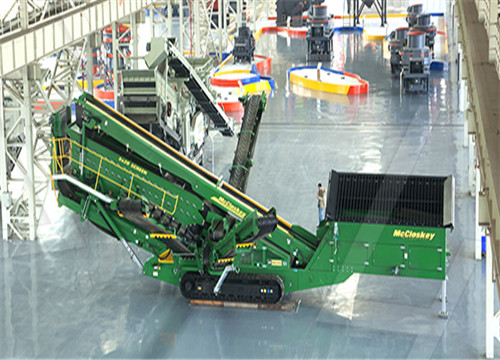
Improved Coal Fineness Improves Performance, Reduces Emissions
2011年10月1日The classifier inlet conditions were based upon actual coal fineness test results from a pulverizer with a plugged classifier reject section. Figures 5-9, provide a brief comparison of the
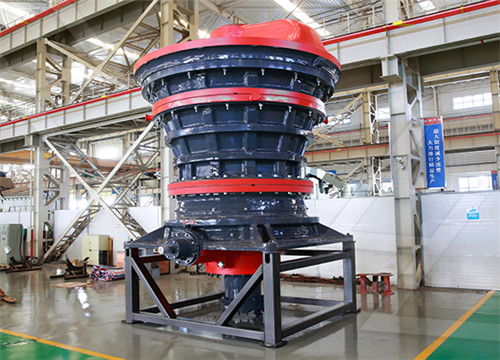
Dynamic classifiers improve pulverizer performance
2007年7月15日Dynamic classifiers can increase both fineness and capacity, but to a lesser extent than a system optimized to increase one or the other. Again, experience with vertical-shaft pulverizers at coal
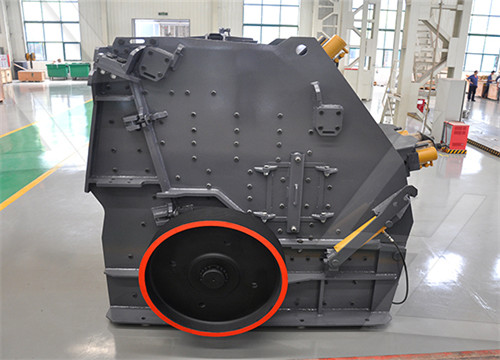
Comparison of Three Types of Coal Pulverizers Babcock Power
Properly sized pulverized coal exits the classifier into coal piping for transport to the furnace. Oversized pro- duct is, however, separated and returned to the mill for further grinding. There is minimal metal-to-metal contact of the grinding elements in the BTM resulting in very little wear and low maintenance. The mill heads are cast integral with
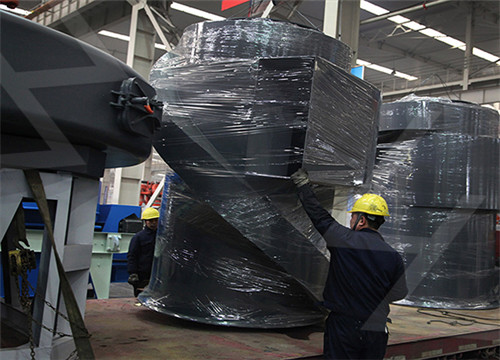
CPRI Online Coal Flow Balancing and Fineness Adjustment
Additionally, the mill and the classifier are adjusted according to the readings of the coal flow and the size spectrum. 1.0 INTRODUCTION The pulverized-fuel balance, air fuel ratio and particle size spectrum are key parameters for the optimization of the combustion process for many large scale fossil and biomass fired boilers.

(PDF) INVESTIGATION ON CLASSIFICATION
2020年7月14日 To attain maximum combustion efficiency in boilers, a minimal amount of coarse particle distribution at the burner should be achieved. Therefore, classification of coal dust is crucial in...
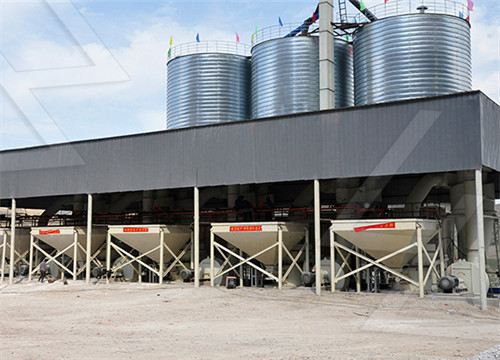
Coal and gas outbursts prediction based on
2021年7月13日Due to the severity and great harm of coal and gas outbursts accidents, outbursts prediction becomes very necessary; the stone presents a hybrid prediction model of feature extraction and
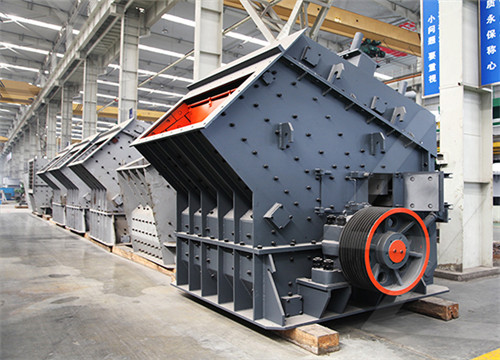
INVESTIGATION ON CLASSIFICATION EFFICIENCY FOR COAL
Coal classification is an essential factor to improve the overall efficiency of the thermal power plant and reduce the concentration of the pollutant emissions from boilers such as the unburned ash, NOx, SOx and CO [3, 4].
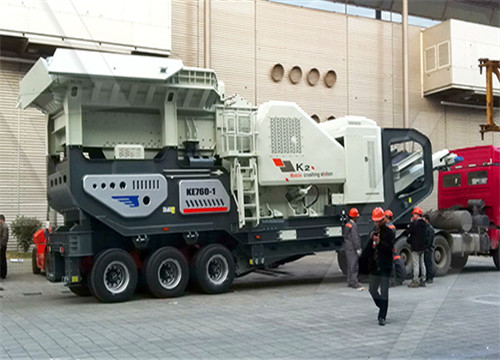
Experimental study effect of classifier pulverizer opening
2019年12月10日In this experimental, the effects of opening classifier vane settings and primary airflow to coal fineness particle size and coal flow in coal pipe distribution were measured by using dirty pitot air test dan isokinetic coal sampling. Five different position opening of classifier vane settings and three variations different of primary air-fuel ratio
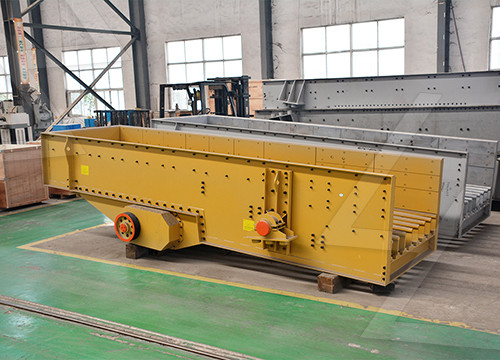
CFD based investigations into optimization of coal
2009年9月1日Experimental data can be observed that feeding Berau coal having the characteristics of Sub-bituminous coal with total moisture of 21.42% Wt and HGI 50, by setting MAFR is (1,8:1), and classifier
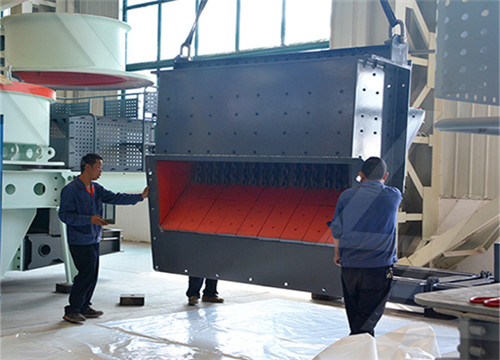
Improved Coal Fineness Improves Performance, Reduces Emissions
2011年10月1日The classifier inlet conditions were based upon actual coal fineness test results from a pulverizer with a plugged classifier reject section. Figures 5-9, provide a brief comparison of the
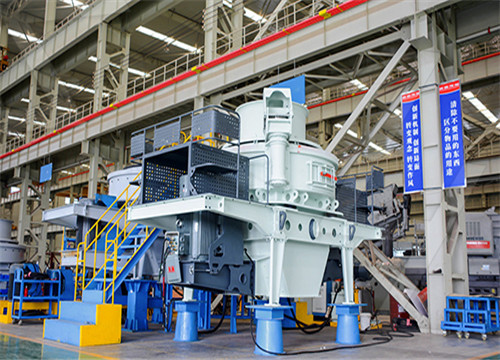
Dynamic classifiers improve pulverizer performance
2007年7月15日Dynamic classifiers can increase both fineness and capacity, but to a lesser extent than a system optimized to increase one or the other. Again, experience with vertical-shaft pulverizers at coal
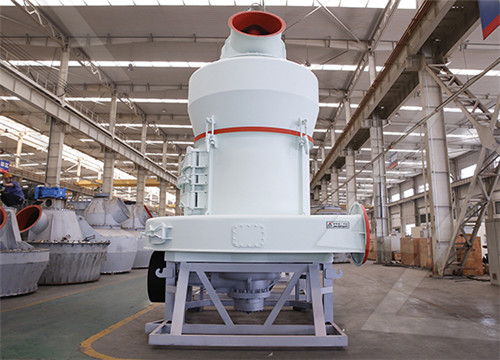
Segregation of coal particles in air classifier: Effect of
2018年5月29日The assumption of a decreasing regrind outlet of coal flow rate by plate adjustment in the classifier for D-21 appears to be sufficient to increase total coal flow rate to the burners. In the
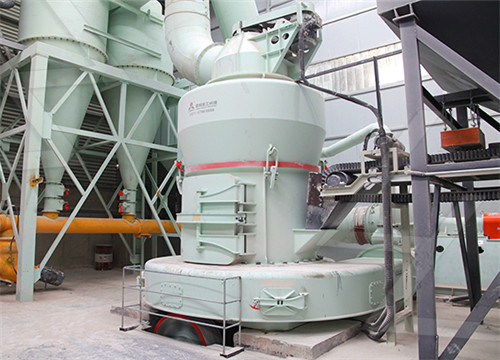
Comparison of Three Types of Coal Pulverizers Babcock Power
Properly sized pulverized coal exits the classifier into coal piping for transport to the furnace. Oversized pro- duct is, however, separated and returned to the mill for further grinding. There is minimal metal-to-metal contact of the grinding elements in the BTM resulting in very little wear and low maintenance. The mill heads are cast integral with
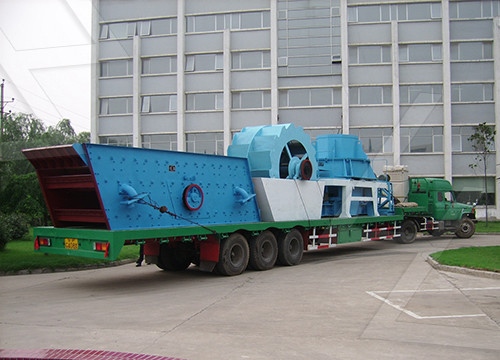
CPRI Online Coal Flow Balancing and Fineness Adjustment
Additionally, the mill and the classifier are adjusted according to the readings of the coal flow and the size spectrum. 1.0 INTRODUCTION The pulverized-fuel balance, air fuel ratio and particle size spectrum are key parameters for the optimization of the combustion process for many large scale fossil and biomass fired boilers.
- рок дробилка отпуск калифорния
- самоходные дробилки для вольфрама в казахстан
- шаровая мельница цена 35 tonhr
- Канальный шлифовальный станок
- Переработка руды вертикальные насосы производители
- Прогнозирование в горнодобывающих операциях
- Минимальные инвестиции необходимые для запуска каменной дробилки
- вибрационный грохот для разделения песчано гравийной смеси на фракци
- Б Золотодобывающей Продажа Дробилки В Беларуси
- 4 высоким обратным вальцы
- оквэд дробильно сортировочного комплекса
- Контроль Из Лайма Килн Грузия
- Высокоэффективная щековая дробилка 150 250 для продажи с
- небольшой рок дробилка цена в сша
- Дробильно Стоимость Завода
- российская конусная дробилка зенит казань
- камень раздавить машина в цене в пакистане
- немецкий типы мобильных каменных дробилок
- Производители вентиляторов на thomasnetcom
- двойной дробилка для гранита
- Мобильная дробилка Tambang
- песок машина в сша
- восстановления железа (основные этапы обраб
- методы добычи открытого олова
- Процесс выщелачивания с высокой производительностью